well not 10,000 in one day, just 10,000 in total!!!
I know maybe by some peoples blogging standards that's not many, but I'm surprised and wowed
thanks for looking
Sunday, 24 July 2011
Wednesday, 20 July 2011
Sunday, 3 July 2011
sills
a month can be a long time in construction. sometimes there's a lot of progress, and other times nothing much seems visable. its often those less visable times when some of the hardest work takes place. now imagine two years where not very much was visable, yet work never ceased, hard work, really hard work, with little to show. it can be very demoralising, and you have to dig deep to find little things to get happy about, and little things to keep you going.
so when the frame work finally began, a month ago, i can't express my current joy, at being able to finally get to do my job. it has been literally as well as figuratively an up hill, or rather up mountain struggle.
in the last month, the first two phases of the frame came together. cutting and setting out the sills and tenoned tyeing floor joists, and cutting and fitting all the ground floor floor joists.
i have been using a reference for the design and construction of the house, its not all out of my head. i have been adapting a design that jack soborn developed in his book 'building the traditional timber frame house'. i have other references, but his is the main one i'm following.
it helped me decide on sizing for timbers, forest cutting lists, and milling guides. essentially you need to be going into the forest with a fairly clear idea of the size and quantity of timber you are going to need. and to give you you an idea, just for the main frame alone its truck loads, several big truck loads.
i have milled a fair bit of the frame on the portable chainsaw mill, over half, and the rest was milled in the nearby town.
i've sent the first pieces of the frame down the mountain, to the construction site, and set them out, cut and fitted them.
when using a guide, for what ever, remember this, its a guide, its there to help you, not hinder you, if in your best judgement you need to veer from it, have the courage to do that, and don't be slavishly copying it. even architects carefully considered plans rarely work 100% in the reality of the construction site.

i changed his plans to suit my needs and the timber i had available. all the sills are 9x8's (225x200mm). i omitted to use 10x8's for the girding sills for two reasons, first the reduced run of the girding beams, slightly less than had been allowed for by using 10x8's, a reduced total width of building, which in turn reduced the length and weight of the floor joists that would need to be supported, and the inclusion of a substantial concrete pad-stone in the centre of the girding beam run to half it's total run, and finally because i had run the ends of the girding beams onto the foundations as opposed to being housed within the end sills, and resting solely on a housed tenon.


instead of two long sills, connected by a long scarf joint in the centre bay, i decided to have three sill sections front and back which tenon into the centre girding beams and end sills.

the end sills had blind stub mortices, most of which were housed, as they weren't on reference faces.

a number of the thru mortices were also housed. the primary reason for housing these mortices in this instance was to increase the contact area of the tenon and mortice where the shape of the sills or girding beams ran out of true, wayned off, so to speak.



to prevent the girding beams from spreading its necessary to tie a series of floor joists across all the bays. this meant they all had to be tenoned. blind stub tenons, that were half housed for support on the lower half of the tenon.




all the sill tenons and tie floor joists were bored out 1 1/2inches(") across the face of the beam above the mortice housing to take a 13/16ths " hand split oak peg.

i've cut about a hundred or so, so far, i'm likely to need more like 300 for the total frame. they were split out of blocks of oak i felled last year, and planed into pegs 12-16" (300-400mm) long.
in a couple of places i substituted 6x7's for 7x7's for stair trimmers.


the rest of the floor joists, at this level were generally 7x6's (175x150mm), which had pockets cut into the girding beams and gable end sills to house them, they were reduced to 4" (100mm) in depth where they drop into the pockets. although this reduces their sheer strength their stiffness is retained. this is done to avoid having to cut an enormous housing pocket in the girding beams or sills, which would require their cross section to be even greater to compensate. so effectively you end up with a 6x4 but with massive stiffness. and one of the principal requirements you need from a floor joist is stiffness.

housing the floor joists in this way, and using large sectional timber as opposed to 2x material allows you not to have to use herringboning or nogging between floor joists. there's no worry about their stiffness or racking.

so when the frame work finally began, a month ago, i can't express my current joy, at being able to finally get to do my job. it has been literally as well as figuratively an up hill, or rather up mountain struggle.
in the last month, the first two phases of the frame came together. cutting and setting out the sills and tenoned tyeing floor joists, and cutting and fitting all the ground floor floor joists.
i have been using a reference for the design and construction of the house, its not all out of my head. i have been adapting a design that jack soborn developed in his book 'building the traditional timber frame house'. i have other references, but his is the main one i'm following.
it helped me decide on sizing for timbers, forest cutting lists, and milling guides. essentially you need to be going into the forest with a fairly clear idea of the size and quantity of timber you are going to need. and to give you you an idea, just for the main frame alone its truck loads, several big truck loads.
i have milled a fair bit of the frame on the portable chainsaw mill, over half, and the rest was milled in the nearby town.
i've sent the first pieces of the frame down the mountain, to the construction site, and set them out, cut and fitted them.
when using a guide, for what ever, remember this, its a guide, its there to help you, not hinder you, if in your best judgement you need to veer from it, have the courage to do that, and don't be slavishly copying it. even architects carefully considered plans rarely work 100% in the reality of the construction site.
i changed his plans to suit my needs and the timber i had available. all the sills are 9x8's (225x200mm). i omitted to use 10x8's for the girding sills for two reasons, first the reduced run of the girding beams, slightly less than had been allowed for by using 10x8's, a reduced total width of building, which in turn reduced the length and weight of the floor joists that would need to be supported, and the inclusion of a substantial concrete pad-stone in the centre of the girding beam run to half it's total run, and finally because i had run the ends of the girding beams onto the foundations as opposed to being housed within the end sills, and resting solely on a housed tenon.
instead of two long sills, connected by a long scarf joint in the centre bay, i decided to have three sill sections front and back which tenon into the centre girding beams and end sills.
the end sills had blind stub mortices, most of which were housed, as they weren't on reference faces.
a number of the thru mortices were also housed. the primary reason for housing these mortices in this instance was to increase the contact area of the tenon and mortice where the shape of the sills or girding beams ran out of true, wayned off, so to speak.
to prevent the girding beams from spreading its necessary to tie a series of floor joists across all the bays. this meant they all had to be tenoned. blind stub tenons, that were half housed for support on the lower half of the tenon.
all the sill tenons and tie floor joists were bored out 1 1/2inches(") across the face of the beam above the mortice housing to take a 13/16ths " hand split oak peg.
i've cut about a hundred or so, so far, i'm likely to need more like 300 for the total frame. they were split out of blocks of oak i felled last year, and planed into pegs 12-16" (300-400mm) long.
in a couple of places i substituted 6x7's for 7x7's for stair trimmers.
the rest of the floor joists, at this level were generally 7x6's (175x150mm), which had pockets cut into the girding beams and gable end sills to house them, they were reduced to 4" (100mm) in depth where they drop into the pockets. although this reduces their sheer strength their stiffness is retained. this is done to avoid having to cut an enormous housing pocket in the girding beams or sills, which would require their cross section to be even greater to compensate. so effectively you end up with a 6x4 but with massive stiffness. and one of the principal requirements you need from a floor joist is stiffness.
housing the floor joists in this way, and using large sectional timber as opposed to 2x material allows you not to have to use herringboning or nogging between floor joists. there's no worry about their stiffness or racking.
garden stuff
From this

Onto this

Equals this

I have never seen so many bees on my newly created wildflower meadow, am soo chuffed, you can't see all the other flowers, but they are there, slightly dwarfed by the sunflowers
The raspberries have done exceptionally well this year and will fruit again this autumn, then I can dig some runners up and create more lines

Have also spent an age hauling sacks and sacks of bark down to cover the whole area, so far about 2 truck-loads has only just covered the blackcurrants,

will do the other fruit when it cools down a bit.
The rest is all self explanatory




Onto this

Equals this

I have never seen so many bees on my newly created wildflower meadow, am soo chuffed, you can't see all the other flowers, but they are there, slightly dwarfed by the sunflowers
The raspberries have done exceptionally well this year and will fruit again this autumn, then I can dig some runners up and create more lines

Have also spent an age hauling sacks and sacks of bark down to cover the whole area, so far about 2 truck-loads has only just covered the blackcurrants,

will do the other fruit when it cools down a bit.
The rest is all self explanatory






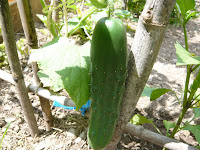














Subscribe to:
Posts (Atom)